View Pdf » EN
Vacuum for Beverage Can Production at Ball Packaging
The manufacturing of aluminium cans for the beverage industry is strongly dependent on vacuum. Aluminium is a non-magnetic material and vacuum assists the Pick and Place high-speed processes by holding the cans tightly during different stages. The introduction of the Pneumofore UV Series vacuum pumps has been greatly appreciated at the Wakefield plant of Ball Packaging since 2000. In 2017, the upgrade of the existing vacuum system further optimized performance and brought considerable energy savings.
Before the introduction of Pneumofore technology, vacuum installations at this plant were based on other technologies, such as screw pumps. But screw machines run at high speeds, driven by a gear box that includes a minimum of six bearings. Over time their poor performance lead to obvious consequences. Beyond the excessive power consumption, the customer highlighted the excessive cost of screw air-end overhauling and the frequent maintenance needs.
While the evacuated air is quite pure, can production needs up to 9.000 m3/h capacity for 24/7, year-long operation. This prerequisite makes equipment reliability and durability crucial to prevent the enormous losses caused by a vacuum pump break down. Ball Packaging became a Pneumofore customer when they realized the benefits of the UV Series rotary vane vacuum solution rather than other technologies.
Initially, Ball Packaging replaced previous vacuum pumps with five Pneumofore UV30 units in 2000. At that time, the UV30 were the largest air-cooled rotary vane vacuum pumps in the world. Thanks to their low rotation speed and correspondingly low operating temperature, in a very short period the UV vacuum pumps largely outperformed screw pumps by far in terms of their operational costs and spare parts durability. The customer also benefited from a reduced environmental impact and Pneumofore’s ability to engineer and design bespoke solutions.
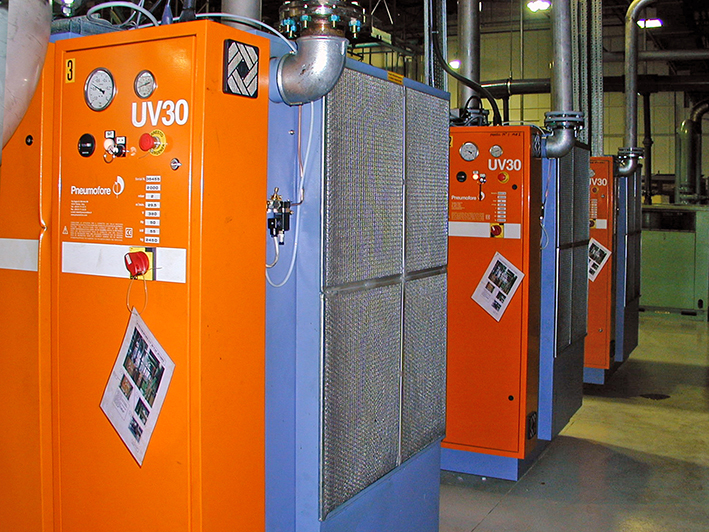
The UV30 pumps installed in 2000 worked 24/7 for 16 years
The UV30 pumps operated non-stop for 16 years, which means around 130.000 hours of operation for each unit, with very low maintenance and no air end overhauling requirements. In 2017, the engineering department of Ball Packaging decided to upgrade the centralized vacuum system by changing the configuration and introducing Variable Frequency Drives.
The upgraded system is made of three UV50 VS90 vacuum pumps, which are the largest air cooled, single stage units available for can production. The simplified configuration and the extended maintenance intervals of 8.000 hours of continuous operation brought savings to the maintenance annual cost, as shown in the below table. Furthermore, the Variable Speed option improved the vacuum setting control with consistent energy savings during low production peaks with the total average consumption reduced by 48%.